Process capability study and index, how to calculate Cp & Cpk
Process capability is mathematical & statistical study for determine the processes are performing by its natural variations and capability. In Process carry out for calculating Cp & Cpk for understand the variations in the processes by index.
Introduction to Process capability
The process capability study is conduct for the identify variation in processes and capability to ensure the product met customer technical requirements. This study performs with all the manufacturing processes individually. Where all the process parameters and criteria are conducts for study. Management establish procedure for improve the process.
In this study, engineers can analyze the processes, to ensure processes are performing its natural variations or not. The study includes capability of processes whether process is able to maintain customer expected specification and technical requirements or not.
How to perform process capability study?
The department head is responsible for prepare & implement process capability study at all related places. The study also expecting the manager frequently monitor & control over activities. Related document verification and reviews are includes in study procedure.
The begging of the procedure is from production planning department. Planning team should be understand and clearly mentioned in the planning sheet of the customer requirements for product. The details of planning sheet may includes product characteristics, specifications, quantity and specific requirements. According to customer requirements the study should be mentioned.
Study inputs & processing
The study is conduct as on collection of product quantity from various time intervals on particular day. Product Dimensions, measurement criteria, are necessary for process capability analysis. Team is verify requirements and prepare process capability study plan. See picture below for process capability plan:
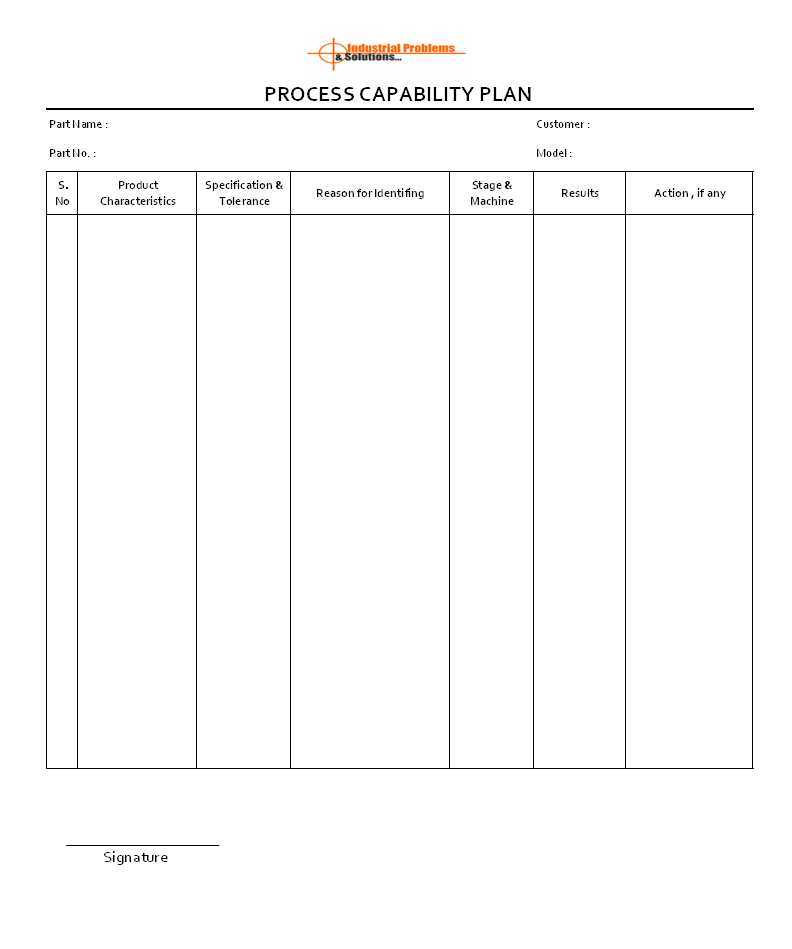
The process capability plan
The study plan is managed to considering requirements, such as product characteristics, specifications and acceptable tolerance. The study may also includes the product standard tolerances, stages of process, study results of machine etc. Team Prepare schedules and plan in this plan sheet.
The study of process capability is conduct on specific formulations. The calculate Cp index which is ratio of the specification allowable to dimension of process special characteristics. Which is “six sigma” standard deviation formulation.
The production team actively participate in the study for identification of the critical components in the processes. The process capability study should carried out in the variation allowable as sigma variation. Production team conduct plan for improvement the process as acceptable level. That should be according to the six sigma requirements.
How to caculate Cp & CpK Index
the process capability study should carried out in the variation allowable, and the as sigma variation. The production concern peoples are manage plan to develop and improvement the process as acceptable level that is six sigma requirements and accordingly.
Calculate Cp index which is the ratio of the specification allowable to the width of the distribution of the process characteristic (six standard deviation)
Cp
Cp = Specification Allowable / Process Width
= (USL-LSL)/ (6 x Sigma)
Where USL – Upper specification limit & LSL – Lower specification limit.
CpK
CpK = (X bar – LSL) / (3 x Sigma) or (USL-X bar) / (3 x sigma)
For a two-sided specification, CpK is the ratio of the distance from the nearest specification limit to the process average, divided by three standard deviations.
CpK = Minimum of { [(USL-X bar) / (3 x sigma)] or
[(X bar-LSL) / (3 x sigma)] }
For a two-sided specification, CpK is the ratio of the distance from the nearest specification limit to the process average, divided by three standard deviations.
CpK = Minimum of { [(USL-X bar) / (3 x sigma)] or
[(X bar-LSL) / (3 x sigma)] }
Interpretation of Cp and CpK index values:
- If Cp < 1 then the process variation exceeds specification (Defectives are being made)
- If Cp = 1 then the process is just meeting specification (A minimum of 0.3 % defectives will be made, more if the process is not centered)
- If Cp > 1 then the process variation is less than specification, however, defectives might be made if the process is not centered on the target value.
Verify The capability
- If CpK < 1 .33then the process is not capable
- If CpK = 1.33 to 1.67 then the process is marginally capable
- If CpK = 1.67 to 3 then the process is capable
- If CpK > 3 then the process capability is excellent; it is highly capable
Compare the results
- If Cp is high and CpK is high then process is stable and in control (Maintain the centrality)
If Cp is high and CpK is low then the process is potentially capable but the process performance is not adequate (Aim for centrality of the process with reference to the specification mean) - If Cp is low and CpK is low then improvements needed to make the process potentially capable (Reduce process variability or seek alternate process, m/c etc.)