System improvements, enhance the resources reliability and system value
Improving critical element in system, that can improve overall performance of the system as well as possible to controls over non-conformity which raised due to unexpected causes.
System improvement through Corrective & Preventive actions
The article describes the format system improvement in organization. Corrective and preventive actions activities are also considering as system improvement. And here we are talk about the important part which is the part of system improvement. That is corrective and preventive actions.
Coordination of Corrective and preventive actions
This article covers corrective actions and preventive actions and continuous improvement activities. Generally, any employee in the organization may propose initiation of a corrective or preventive action. The system improvement coordinator maintains the system improvement tracking system. It is the responsibility of all department managers to assure that, this procedure is being properly follow. It is the responsibility of the appropriate Manager to assure that the corrective or preventive action is implement and effective in their department.
How to implement corrective actions and preventive actions on non-conformity
Corrective Action are actions taken to eliminate the causes of an existing nonconformity, defect or other undesirable situation in order to prevent recurrence of the issue. Preventive Action are actions taken to eliminate the potential occurrence of non-conformity, defect or other undesirable situation.
Who is System coordinator?
The system improvement coordinator is the person who oversee the corrective or preventive action system. They are not responsible for determination or implementation of the action, but they oversee the system as state in this procedure. The system improvement coordinator for all corrective and preventive actions is the Administrations Manager or designee.
How to perform Initiation of a Corrective Actions and preventive actions?
- Corrective Actions and preventive actions may be initiate due to a result of, but not limit.
- Results or initiation from management review.
- Customer complaint/corrective action requests.
- Product nonconformity identification
- Design review, nonconformity identification or issues.
- Process or operation problems and issues
- Supplier or subcontractor non-conformity or non-compliance with Organization or other requirements.
- Non-conformance or observations call out by an internal or third party audit.
- Review of procedures or work instructions.
- Opportunity for improvement.
- Any condition that does not comply with the current ISO 9001 standard.
How to the process requesting and processing it?
All Corrective Actions and preventive actions (Internal, Supplier or Customer) are initiate by requesting a corrective action via email, fax or verbally from the system improvement coordinator. And put in place by issuing and completing System Improvement form and collating a unique folder.
This is system Improvement Log by the system improvement coordinator. The system improvement is then forward this to the appropriate manager, who will review all Corrective Actions and preventive actions requests. And ensure that it is valid and relevant and will then investigate the area. Notify the appropriate person and/or department that will be affect by this corrective actions.
The copy of the system improvement is forward to the responsible person with a copy going to the system improvement Coordinator. The responsible person(s) and/or manager will investigate the issue or problem. To establish main / root cause and shall respond to the system improvement request with the results of the investigation and the action to be taken.
How the internally communicate?
The system improvement coordinator or designee shall follow up within 30 calendar days from the implementation date of the action note in the form. If the corrective action is not effective, the system improvement coordinator shall reject the action and inform the manager. The system improvement remains open to cover further actions, with extensions. If it has not been implement and requires more time, the appropriate Manager will work with the system improvement coordinator to determine the reasons for the action was not implement and an extension shall be agree.
If the corrective action is adequate, the system improvement is approve and sign off by the appropriate manager and close out by the system improvement Coordinator, who also updates the log as require.
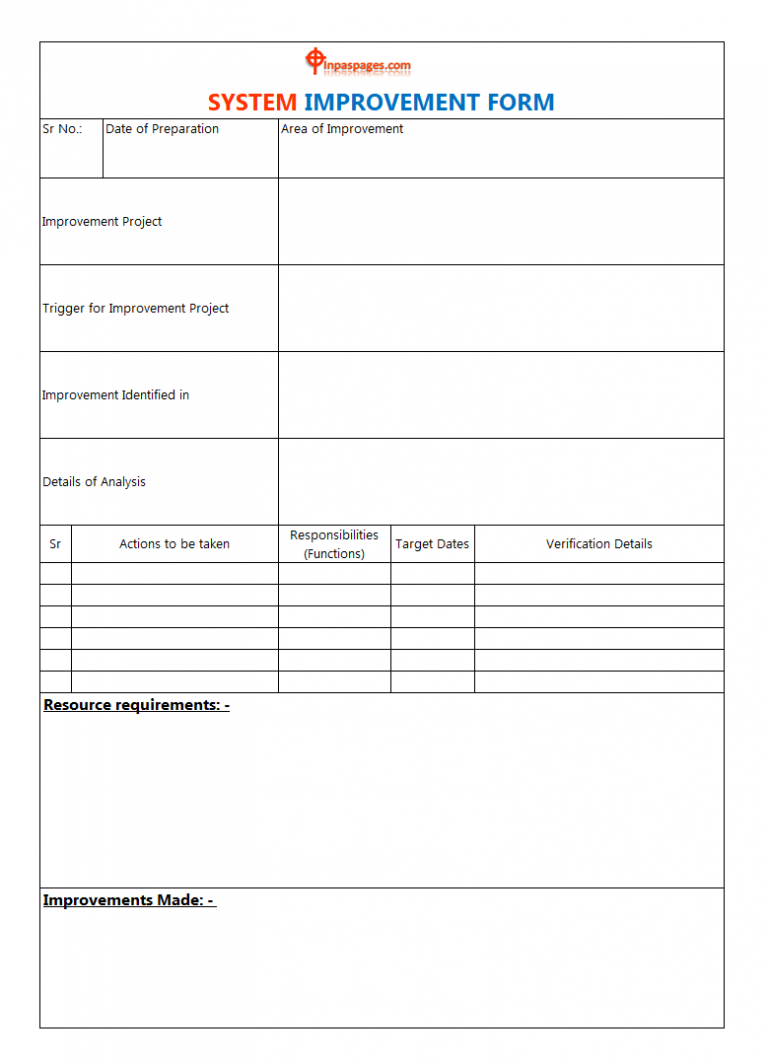
If the system improvement either internal or through a customer, requires a longer period of time. Than working days to implement that may have base on complexity or other issues. The General Manager or designee must approve, sign and date the appropriate system improvement form. The General Manager or designee must also approve any extensions of implementation dates that were originally determine and also sign and date the appropriate system improvement Form.
Focus on Supplier Corrective Actions & Preventive Actions
Supplier Corrective Actions and preventive actions are initiate in the same manner as internal or customer CAPA. It also through Non-Conforming Product/Quarantine if necessary. A copy of the supplier’s response is keep it on file. The Coordinator will work with the appropriate manager to monitor the supplier’s performance. To determine if the action was implement and effective. If the supplier has not respond in 30 calendar days to the corrective action. The appropriate Manager or designee shall take appropriate action. To ensure the problem or non-compliance has been address.
This can affect a Supplier’s Performance Rating. Further evaluation through additional departments or groups may be perform to determine. If the corrective action was implement and effective. If the supplier’s corrective action was not effective, then the corrective action shall be extend & readdress until the problem is resolve.