How to implement Corrective action Preventive action?
To concentrate opportunities for improvement by detecting root cause of a problem and influential alterations to work processes to improve the delivery of services and tasks.
Overview to Corrective action Preventive action
Corrective actions preventive action process is conduct for identify and fix the cause of problem. The procedure is can use to determine root cause analysis. Its usual quality manager is responsible for implement the process which is directly affects the quality of products. But at overall implementation, general manager is equally responsible for it. They are establish this procedures as well monitor and control the activities, to ensure the corrective and preventive actions are effectively implemented.
The management is assign the duties to any person who handle the corrective and preventive actions and responsible for conducting the investigation for identifications and determine the proper root causes, to define the corrective actions and preventive actions planning and scheduling to help in determining and implement its effectiveness. Hence the quality manager is responsible for modifications and updating the internal quality management system documentations and quality manual to reflect corrective actions and preventive action plans and schedules.
Implementation phase:
The quality assurance team is performing corrective actions plan as on initiated by quality assurance team leader to considering significant non-conformance which identified during internal or external audit and management reviews of internal management system. Quality manager is conduct the analysis and implementation process. Team determine the severity, priority and impact on the various processes, activities, and workplaces.
The corrective actions plan is implementing by the appointee, the draft copy prepared and submit to the quality manager for the reviews and identification of requirements for implementation. Hence the quality manager is responsible for the verification the effectiveness of the corrective actions and preventive actions implementation on completion and verified through collection of documented objective evidences.
See example, corrective actions & preventive actions – CAPA implementation form
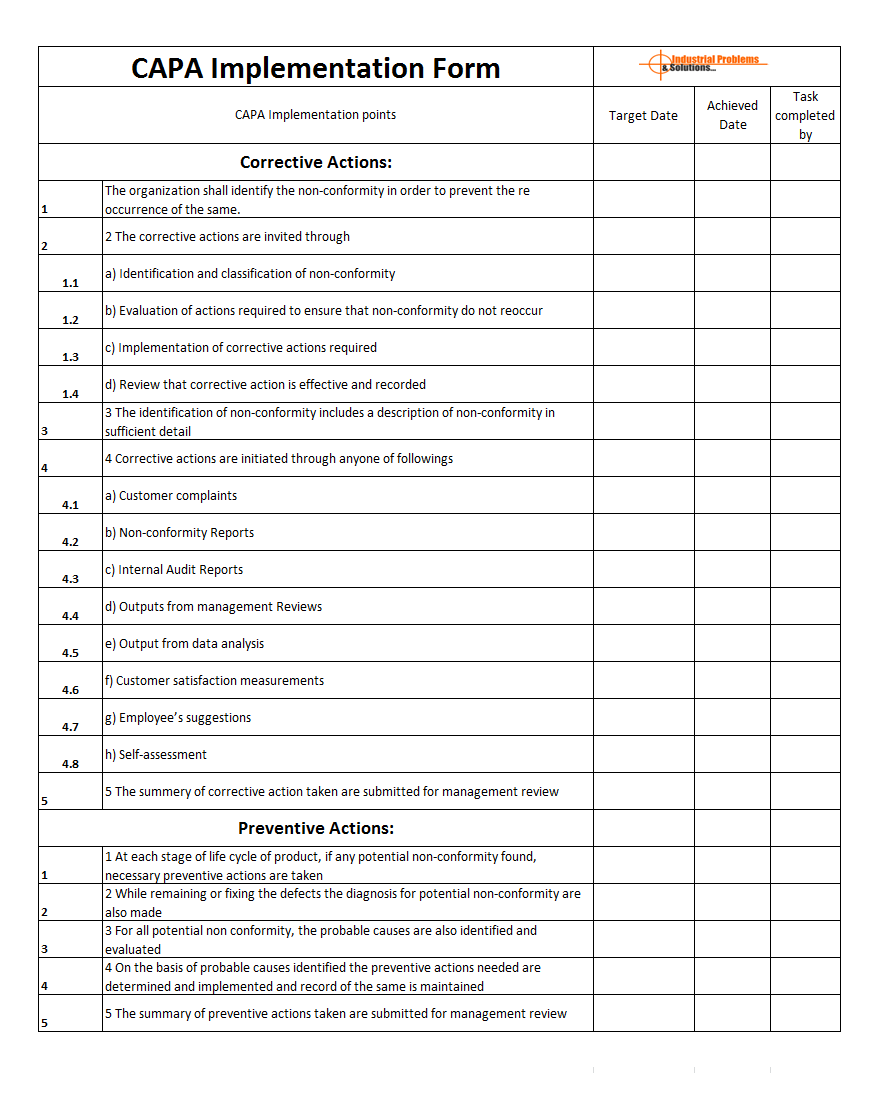
Quality manager is manage implementation related documents includes capa and action plans. The format is used as standards format and recorded in quality system index to easier for implement and makes its in uniform.
See some points that helps to implement corrective actions and preventive actions in organization:
Corrective Actions:
- The organization shall identify the non-conformity in order to prevent the re occurrence of the same.
- The corrective actions are invited through
a) Identification and classification of non-conformity
b) Evaluation of actions required to ensure that non-conformity do not reoccur
c) Implementation of corrective actions required
d) Review that corrective action is effective and recorded - The identification of non-conformity includes a description of non-conformity in sufficient details
- Corrective actions are initiated through anyone of followings:
- Customer complaints
- Non-conformity Reports
- Internal Audit Reports
- Outputs from management Reviews
- Output from data analysis
- Customer satisfaction measurements
- Employee’s suggestions
- Self-assessment
- The summery of corrective action taken are submitted for management review
Preventive Actions:
- In case potential non-conformity is identify at any stage of life cycle of product, its necessary to take necessary actions immediately.
- While remaining or fixing the defects the diagnosis for potential non-conformity are also made
- For all potential non conformity, the probable causes are also identify and evaluate.
- On the basis of probable causes identify the preventive actions needs to determine, implement and record.
- All the preventive actions’ review are taken for reviews in management review meeting.
———————————————————————————————
Download format in word document | Excel Sheet | PDF format
CAPA implementation form
———————————————————————————————