Returned material process management
Returned material process management is to manage corrective action or storage and disposal for the returned of materials to supplied to customer.
The purpose of the returned material process management is establish, maintain, monitoring and control over the transitions made due to returned material by customer which is supplied, the system helps to outline the corrective actions for the returned materials after supply to a customer. In the returned material process management all the incoming material are inspected to identify the problems and match with specifications are given by customers, international specification for the product and technical specifications which are internally used by quality department, in case not match and customer claim is definite that need analysis of product by root cause analysis to find out the fact reason behind the product defects, on base of the identified cause and its action impact to other process as preventive actions to eliminate mistake before become defects in manufacturing processes.
Returned materials from the customers are handing, storage and disposal are conducted by material storage department, material storage department is interact with the quality department for the inspecting the material to identify the defect causes for the further actions, quality inspection and certification responsibility of quality department in case the material possible to recovered by rework that material will be deliver to production for the reproduction for the corrective actions. In returned material management most important part is quality checking / laboratory inspection is prime role and whole management is depends on quality inspection step, when the quality declare the result over the steps are conducted as appropriate requirements or management defined system.
Returned Material Process
- All the incoming material, sales team is managing transportation as notified by customer of the products to be returned, tracking, monitoring steps and concern communication with transport, purchase team of the customer and other concern issues are conducted by sales team
- When the material is reach to company all the concern required steps are taken by the storage department, handing and documentations are raised as notifications.
- Storage peoples are contact with quality peoples to inspect the material for the identification of defects in the product, quality inspectors are conduct the material along with required specifications and other details are checked, the material is managing and identification of the material’s inspection is conducted on base of the format filled by storage department, the storage department primary information is pass to quality department along with material in the “Returned material quality inspection form” see below picture for the reference:
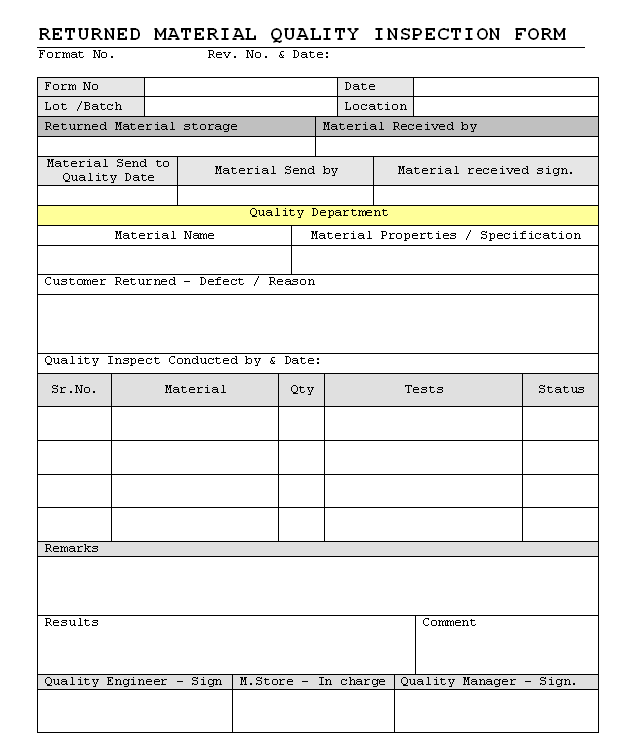
- Quality inspection team is analysis all the material result to identify root cause of the defects & present against management with evidences to possible for eliminate error in manufacturing process or by default from the raw material, in case the material having the raw material defects and exposed at customer end it really not good for company should take necessary actions on raw material procurement and prime inspection on raw material
- Returned material from quality department, material storage is handing and store material as per defined system in storage areas, all the material should be proper labeled, stickers or tagged.
- In case the material is possible to re-work in house transferred by quality for the corrective action on the material for rearrange to dispatch.
Returned material process management is not just managing material after returned from customers but is also playing role to eliminate possibilities of the error in the manufacturing processes to became defect of the product, failure of the product in the manufacturing activities results the loss of the company, hence reputation of the company is also prime objective to maintain reputation in market, customers primary requirements is chipper cost with best quality materials that rejected or defected material cause harm reputation of company.
————————————————————————-
Download Format in Word Document | Excel Sheet | PDF Format
Download Returned material quality inspection form
————————————————————————-