To prevent recurrence of nonconformity, Focus on effective quality management system and deal with analysis of data, frequent audit, system improvement, management reviews and continual improvement.
How to prevent recurrence of nonconformity?
There are many ways to effectively implement the quality system and it can continuously help in improving the system.It is possible through the use of quality objectives, audit results, data analysis, quality policy, improvement measures and preventive actions and management reviews. When we talk about quality management, effective steps can be take to eliminate the cause of non-compatibility to prevent repetition. All actions, correctional actions, can be believed to be appropriate for the performance of non-equality.
Focus on documented procedures
A documented procedure exists to define the requirements for: –
- Reviewing nonconformity.
- Determining the causes of nonconformity.
- Evaluating the need for action to ensure that nonconformity do not recur.
- Determining and implementing actions needed.
- Records of the results of action taken.
- Reviewing corrective actions taken.
Organization takes actions to eliminate the cause of nonconformity in order to prevent re-occurrence. The corrective actions are implemented as a result of analysis information contained on: –
- Customer complaints
- Warranty reports
- Audit reports
- Test reports
- General nonconformity reports
- Any other relevant information.
Managing Analysis and data
As a result of analyzing the above data, the reason for the impact of non-equality and effective measures of organization can be determined. To ensure the desired results have been received, these actions will be analyzed by the quality manager. The organization will make it easier to determine the action needed to avoid the possibility of potential non-relevance to prevent their occurrence. Preventive actions will be appropriate to the effects of the potential problems. A documented procedure exists to define the requirements for: –
- Determining potential nonconformity and their causes.
- Evaluating the need for actions to prevent occurrence of nonconformity.
- Determining and implementing actions needed.
- Records of results of actions taken.
- Reviewing preventive actions taken.
The actions taken in applicable clause will identify areas requiring corrective actions. This will initiate actions to prevent re-occurrences of this type.In addition to the above actions, all the employees of the organization expect to pay attention to any possible non-consistency of the manufacturing manager and / or the quality manager. So effective measures to prevent problems can be implement in the plan. To be sure how these actions affect the quality will be reviewed by the administrator. This review can be done at any time; Internal audits agreed in the audit program will check this area.
General Document:
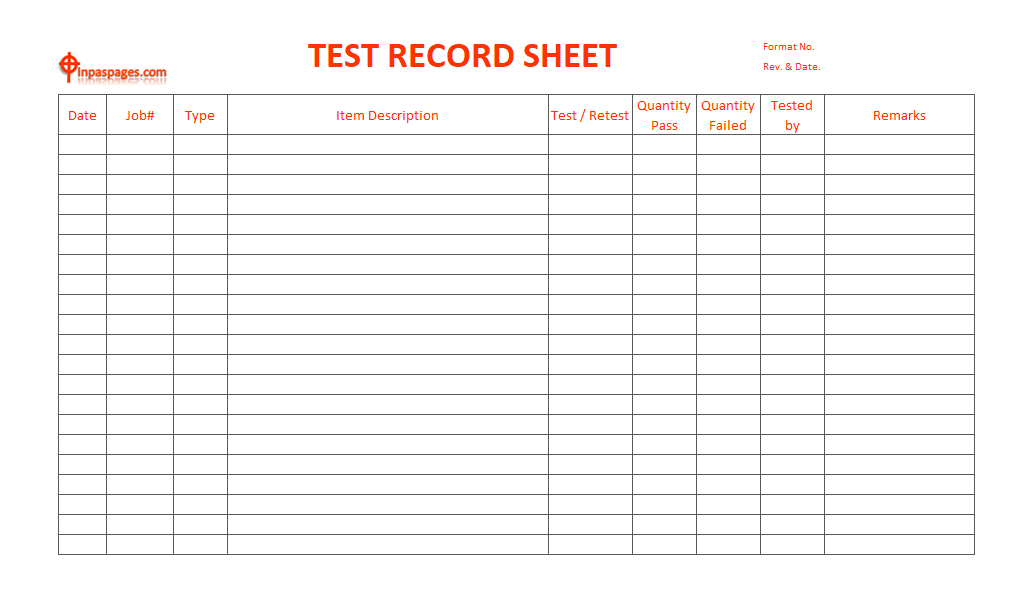