Deviation assessment is process for assess identified deviation in process, process control for prevent deviations and documenting the assessment activities for standardize the system.
Overview
Define the standard procedure that designate identification process.
- Standard operation procedures
- Instructions and methods
- Process parameters, including pre-established.
- Validation / re-validation and values
The deviation case be transitory non-conformity from the operational procedures, equipment, devices, instrument. Its related processes and activities are consider as deviation. The procedure describes and control on deviations. That the affect the product quality, processes or the safety of personnel in workplace. This procedure is sample procedures that helps to implement and apply for the assessment. Reporting concern to deviation within the organization which can directly affecting activities are:
- Raw materials and purchase management.
- manufacturing processes of the product.
- Instruments / equipment / devices and utilities systems and the validation related processes.
- Controls on the processes.
- Management and controls on the final / package product.
- Operation and maintenance of the utilities systems.
- Maintenance tasks at various locations.
- Performance of the actions according to the applicable procedures and delivery of the product.
The quality assurance team is prepare the document, update and implement. The procedure of deviation assessment may also includes in the documentation. Even, in the deviation assessment process, management can jointly operate with quality team. In the preparation of the processes and implementation of documentation are handled according to standard procedures as responsibility assign by management is handle.
How to apply deviation assessment procedure in system?
The non-conformity from the various documentations, procedures, internal system, method or any process parameters at any location of manufacturing / process unit steps are consider as deviations. Which should be include all the installation of machinery, equipment, infrastructure dedicate for manufacturing should be consider accordingly.
The non-conformity are consider in three major classifications: (1) Critical (2) Major (3) Minor.
Critical Type Deviation
The critical type section deviations are considered in case of the non-conforming such deviations may affect the quality of the products. This deviations presenting situations that affecting safety, quality and efficiency. The critical type deviation is serious that needs to more attention to compliance. The define quality and actions including corrective, preventive actions and documentation of deviations to tracking all the activities. As well as present situations.
Major Type Deviation
The major category deviation which is the non-critical deviation are consider. That may lead to the obtainment of the product which may fail to comply specifications. The deviations needs to emergence, corrective & preventive actions that minimize risk to affect the quality of product. The minor categorized deviation needs corrective and preventive action. And have a minimize risk to affect product quality hence each actions should be maintained in separate document that is deviation tracking log:
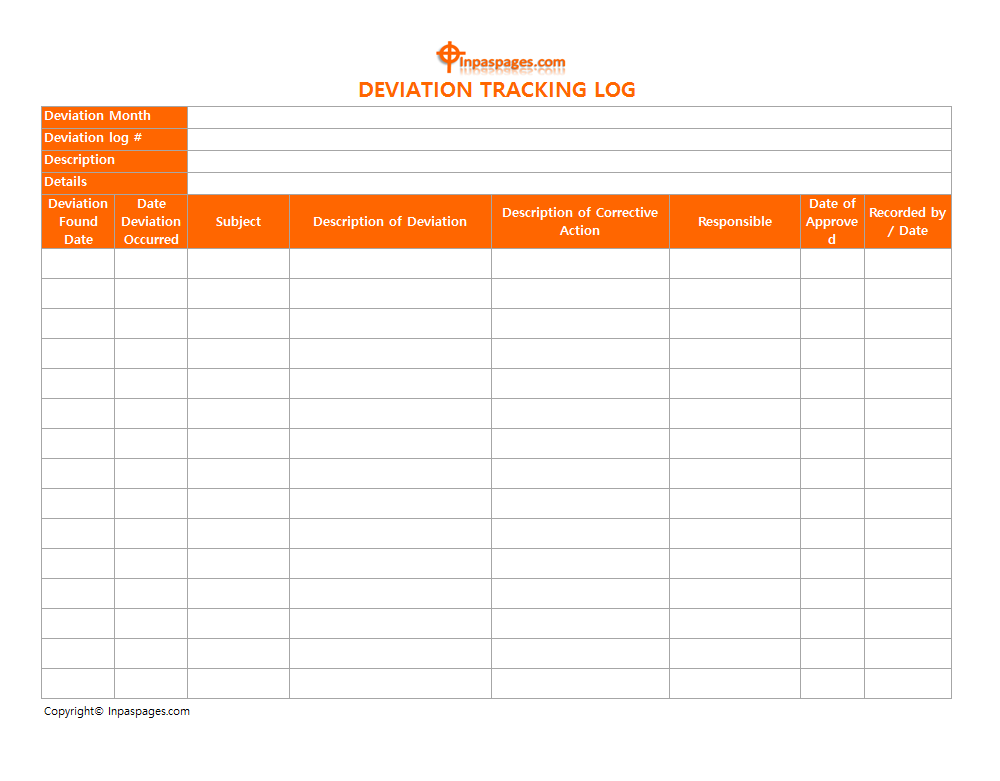
Minor Type Deviation
The minor type of deviations is managing through actions that considered non-critical working parameters. The deviations from the validation, approved condition. Or which that minor specification compliance. The minor deviations need to comply specific requirements. That is corrective and preventive actions and have a low risk to affect the quality of product. The deviation should be properly identified, recorded and should investigated at appropriate location. The deviations results in a non-confirming product, they must be properly documented.
Deviation Reporting
The purpose of the correcting identified deviations & prevention from their recurrence. An investigation that should implement the appearance of the deviation. The methods require for its correction should be initiate. When any employee identify deviation should immediate inform to concern authority that is quality assurance. For the collect the information on the deviation identified. Establish investigation process at appropriate deviation location and occurred where applicable.
In the document management, each reporting should be properly follows by standard operating procedures. That document should be filled out and signed by the person detecting the deviation. Such employee shall describe deviation details and related information. The request of filling details provides to quality assurance team for further action & investigation. Quality assurance team is responsible for collect those information. Categorize risk and deviation as per deviation reporting. Measure the deviation and record information accordingly. The investigations to be carrying out by qualified assurance person with respect of deviation.
Deviation Assessment
The quality assurance department is responsible for identify, categorize, measure of risks levels. Corrective & preventive action as well as monitoring on the processes at appropriate location. Where deviation is identified, the investigation on each deviation should properly maintained are manage accordingly. The deviations shall be review by responsible personnel from quality assurance team. General stages of deviation assessment are:
- The investigation & results through identification, measure & related processes.
- Root causes of each identified deviation.
- Risk Assessment & actions of risk level reduction.
- Determination of the corrective & preventive actions.
- Closing & monitoring.
The team members, the personnel involve in assessment in deviation process should be needs to identify appropriate problems i.e. deviation in the processes. Informs the responsible of the department where person carries activities. The description of each deviation are needs to record it immediate reporting to concern. The quality assurance is responsible for deviation. The identifies are record for quality assurance, and quality assurance team should identify, measure and close the deviation by approving corrective & preventive actions at appropriate levels. The quality assurance responsible for records in the Deviation Tracking Form and classifies the deviations according to the define classification.
Investigation Result
Investigation results carrying out in concern to appropriate deviation should be communicate to the quality assurance team. The deviation reporting is conducts by specialist from the relevant department. All the deviation records should be maintain in deviation reporting, activities, and investigation concern activities.
Which will be affect by such deviation, the results and the conclusions of the investigation. The corrective measures that must be takes to the preventive measure requirments. Hence that other possible deviations should be prevent from occurring and the completion of the investigation.
In case further investigations or processes are remains or needs on after review should be reporting to concern authority for actions. The quality assurance team is verifying that whether the deviation affects the previously produce materials / lots. The affect the future production or not are verifiy by concern authority. On control management & change records should be verifiy each method or processes.